
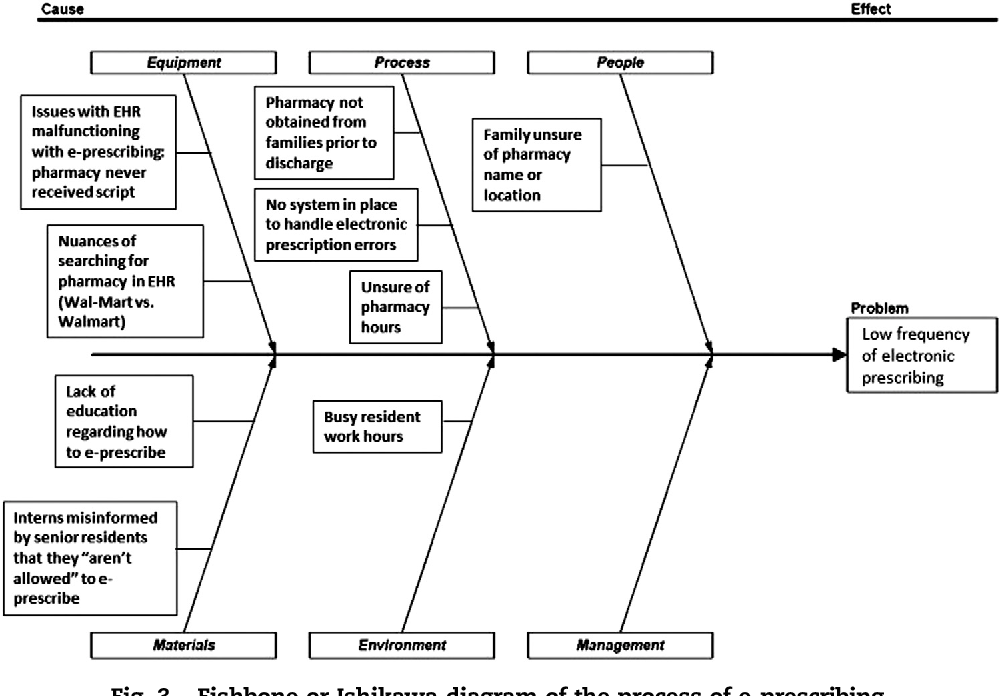
Dr Kaoru Ishikawa, an esteemed quality expert, gave his name to this simple, yet effective problem solving tool. Remember, you can enroll in the FISH Methodology course and begin using this powerful tool right away.The Ishikawa diagram comes under many guises cause and effect diagram or fishbone diagram, but it’s generally referring to the same problem solving tool. There are many different ways of using the fishbone diagram but the 4 steps above should help you get started.
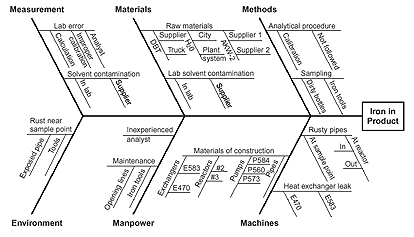
Once you have received the answer ask why again until you have reached the " root cause. A good practice is to ask the individual that identified the problem why did that happen? Then wait for the answer (at the gemba if possible). Once all the possible causes are in the appropriate category begin asking why.
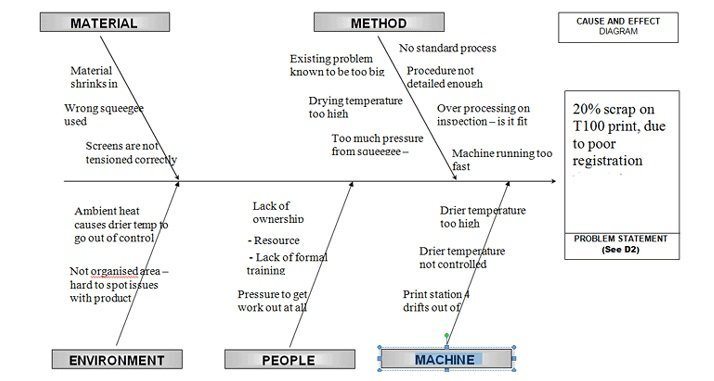
Step 4 - Though the 5 whys are not exactly a part of the cause and effect diagram, the two work together quite effectively.After it has been placed under the appropriate category it will then be time to start "digging." If a cause is identified and the team agrees on the cause, draw a line on the appropriate categories/bone and label the cause. The brainstorming will be focused on identifying possible causes that are associated with the effect. Step 3 - The next step is to begin brainstorming with your team.Please remember though, no fishbone diagram is set in stone so your team should pick the most appropriate categories for the problem you are trying to solve. As a reminder the 6M or 8M fish bones are widely accepted in manufacturing, the 7P is commonly used in transnational or marketing situations and the final type of ishikawa diagram is the 5S diagram. These are the categories that we talked about earlier on. Step 2 - Once you have clearly defined a problem and gained consensus from any team member who might be involved it is now time to start building the "bones" of our fish.This can take a bit of practice as often times the initial problem may not be revealed right away. Some examples of the effect maybe quality issues that aren't meeting a standard or a particular process that does not meet the required metrics. Step 1 - Clearly define your effect or the problem you are trying to solve.Here is a general process that you can follow to conduct a root cause analysis. The fishbone diagram is commonly paired with the 5 why analysis in order to drill down to the root cause. Ultimately the categories are based on the team's agreement with possible categories that might be related to the problem that is being analyzed. Although the 6M fishbone and the 8M fishbone are globally recognized as the standard for manufacturing, transactional processes often utilize a 7P fishbone diagram. One of the most common mistakes made with the Ishikawa diagram is the belief that there are set categories for each of the branches. The tool is still used today by many different industries and has proved its worth on many different levels. One of the fundamental tools he used on many of his projects was the ishikawa diagram. Ishikawa pioneered a major quality movement while working at Kawasaki. The ishikawa diagram was founded in 1968 by Kaoru Ishikawa.
